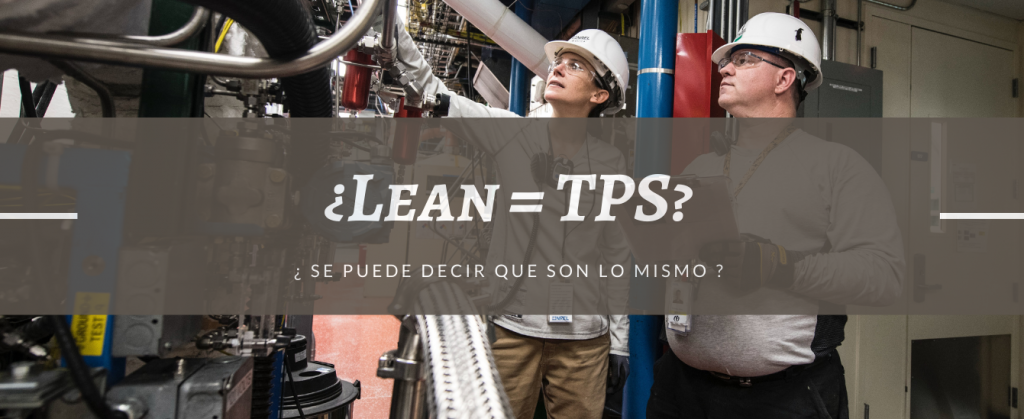
¿Puede decirse que Lean es lo mismo que TPS?
Es relativamente común leer en publicaciones de blog y tutoriales referentes a la mejora continua que Lean es la versión Norteamericana del Sistema de Producción Toyota (TPS). Muchos estudiantes e ingenieros, de manera simplista y equivocada, equiparan una y otra filosofía o sistema. Para comenzar, es importante dejar claro que Lean no hubiese existido sin las bases que plantea el sistema japonés. Si bien Lean adopta y aplica varias de las herramientas planteadas por su sistema predecesor – TPS surge en la década de los 50s finalizando la segunda guerra mundial mientras que Lean solo toma forma hasta los años 90s, existen elementos esenciales desde sus principios hasta el enfoque de mejoramiento que marcan diferencias que no se pueden obviar. Fundamentalmente Lean y TPS no son iguales, aún si comparten algunos objetivos como la generación de valor a través de la eliminación de los desperdicios en los procesos. Eso sí, existen aspectos del Lean Norteamericano que nacieron divergentes de la visión Japonesa y que con los años han ido regresando para asemejarse más a los principios orientales.
Cuadro Comparativo
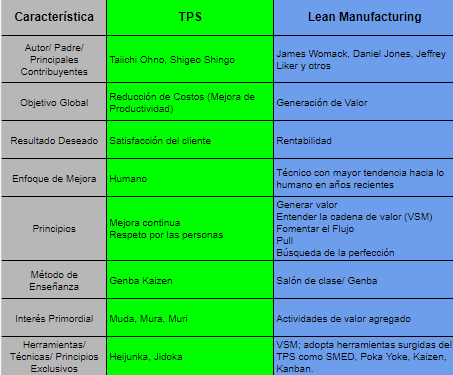
Analizando en detalle los aspectos comparados en la figura, podemos hacer las siguientes anotaciones:
- Mientras TPS menciona explícitamente el respeto por las personas como uno de sus principios, Lean pareciera dejarlo en un segundo plano. Esto no quiere decir que Lean no valore el aporte del trabajo en equipo y el respeto por el colaborador, no obstante si es muy diciente e indicativo del mayor enfoque que pone Lean en el aspecto técnico de la generación de valor para el cliente a través de sus múltiples herramientas. TPS, por otro lado, no deja de lado el aspecto técnico pero coloca el respeto por el colaborador como uno de sus pilares, dando gran importancia al aspecto humano en la consecución de objetivos operativos.
- Sin embargo, es de resaltar que el enfoque casi exclusivo en la rentabilidad que pudo tener Lean en sus inicios y la aparición de desconfianza y resistencia que ello generó ha ido cambiando para darle mayor importancia al aspecto humano. Luego de implementaciones fallidas o de lento avance debido a interpretaciones erróneas de Lean como únicamente un conjunto de herramientas, sin tener en cuenta el factor humano, ha favorecido la adopción de un acercamiento con mayor énfasis en habilidades blandas y trabajo colaborativo para mejorar los resultados de aplicaciones Lean Manufacturing en industria.
- James Womack y Daniel Jones introducen el término Value Stream en su libro Learning to See y ponen en el radar de la mejora continua mundial una herramienta poco utilizada por la división de Toyota Overseas Management Consulting (OMCD), de donde se dice es originaria. La perfeccionan y estandarizan, y hoy por hoy, VSM es una herramienta clave y poderosa de la escuela Lean.
- Lean adopta los 7 desperdicios de la producción -MUDA- planteados por el ingeniero Taiichi Ohno y apunta sus herramientas hacia eliminarlos. Adicional a Muda, TPS por su parte hace énfasis en Mura – Irregularidad, y Muri – Sobrecarga e incorpora herramientas como Heijunka, poco utilizada en su definición Japonesa en el Lean Manufacturing occidental
Si bien aún hoy el enfoque de mejora Lean occidental tiende a estar más orientado hacia las herramientas técnicas que al aspecto humano, resulta evidente que ambos aspectos son esenciales para maximizar las probabilidades de éxito de iniciativas de mejora. Los de la escuela Lean occidental lo han notado, dando mayor relevancia al principio del “respeto a las personas” declarado explícitamente por el Sistema Japonés y reconociendo el punto central de la valoración y empoderamiento del recurso humano para el éxito del sistema. Como se discute en nuestro artículo ¿Es Lean Sinónimo de Recortes de Personal?, si el enfoque exclusivo es la reducción de costos y la rentabilidad, sin tener en cuenta al colaborador, la resistencia y la desconfianza se apoderará no solo de la iniciativa actual sino de proyectos venideros.
Contáctanos en Clockwork Excelencia Operativa para acompañar y asesorar tus proyectos e implementaciones Lean.
Fuentes:
WOMACK, James, JONES, Daniel. Lean Thinking (1996)
OHNO, Taiichi. Toyota Production System (1988)